Fire Suppression Basics: Nozzle Coverage and Location
In case you missed any of the previous posts in the Vehicle Fire Suppression Basics series:
- Blog post 1: Extinguishing Agents
- Blog post 2: Detection Systems
- Blog post 3: Control Module
- Blog post 4: Suppression Agent Tanks
- Blog post 5: Hazard Analysis
Part 6 of 8: Nozzle Coverage and Location
Having identified the fire hazards and areas which require protection, the next step is to determine the number of discharge nozzles needed and where they should be placed to provide the best coverage. This is where the expertise of the fire suppression system designer and installer comes in.
Key Nozzle Considerations
When using any nozzles, it is critical to ensure that obstructions do not interfere with the discharge pattern. However, obstructions that are unavoidable can often be overcome by installing additional nozzles in different locations to ensure complete coverage.
Nozzles must be fitted with blow-off caps to prevent debris such as wood chippings or coal dust entering and clogging the nozzle. When the system is activated, the pressure exerted by the extinguishing agent will remove these caps and begin discharge.
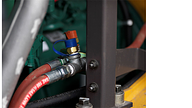
Ardent Dry (red) and Wet (blue) Chemical discharge nozzles with blow-off caps.
It is important to remember that different models of nozzle will vary in their discharge patterns. This allows system designers to avoid wasting any agent and provide coverage specific to the shape and size of the hazard area.
When selecting nozzles and nozzle locations, the following rules apply:
- When choosing the proper nozzle, remember the entire hazard area must be within the nozzle's pattern and maximum effective discharge range.
- Some hazard areas may exceed the area covered by one nozzle and may require additional nozzles for full protection.
- In some cases, a single nozzle can cover more than one hazardous area, such as a transmission and torque converter. This is acceptable, but it is important to remember that the discharge pattern must cover the entirety of all hazard areas.
- When planning nozzle locations, make certain the effective flow of extinguishing agent to all recognised hazard areas will not be obstructed.
- If obstructions cannot be avoided, additional nozzles may be needed to provide complete coverage of the hazard area.
- In areas where the environment may cause extreme build-up of class A materials, such as wood debris, coal dust or oil, it is advised that designers use the largest system tank available and keep nozzles per tank to a minimum. This allows the maximum amount of extinguishing agent per nozzle and gives the longest discharge time.
After completing a hazard analysis and having established nozzle type, quantity and location, the type and quantity of extinguishing agent tanks can be determined. The amount of extinguishing agent should be sufficient to provide each nozzle with the correct flow rate. We will look further into this area in the blog post.
Related News
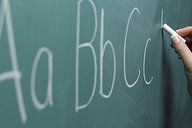
Fire Suppression Basics: Fire Hazard Analysis
In this post, we look at the principles behind a fire hazard analysis and how they dictate system design parameters such as quantity of suppression agent.
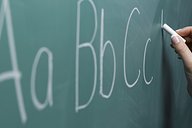
Fire Suppression Basics: Suppression Agent Tanks
No fire suppression system is complete without the correct suppression agent tanks. In this blog post, we look at the two main types of tanks.
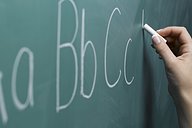
Fire Suppression Basics: Control Systems
Extinguishing agents and detectors are key components of any system, but it is the control module that dictates the response to fire.