Fire Suppression Basics: Suppression Agent Tanks
In case you missed any of the previous posts in this series…
Part 4 of 8: Suppression Agent Tanks
No fire suppression system is complete without the correct suppression agent tanks; they are used to store the suppression agent and play a vital role in the dispersion of the agent upon system activation. In this blog post, we look at the common issues affecting agent tanks and the importance of frequent maintenance and inspection.
Understanding Agent Tank Types
Stored pressure and cartridge operated tanks are commonly use in vehicle fire suppression systems. Both types of agent tank will perform well when used in the right application and environment. However, it is important to understand their key differences.
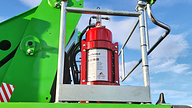
Ardent dry chemical agent tank showing pressure gauge
Stored pressure tanks
In stored pressure tanks, the suppression agent is stored in the same canister as the propellant, typically compressed nitrogen gas. This gas carries the agent from the cylinder, through the nozzles, to the targeted fire hazard area. A pressure gauge is fitted to the tank to allow operators and maintenance personnel to check that the tank is properly pressurised, this can be done by simply verifying that the needle on the gauge is in the green segment.
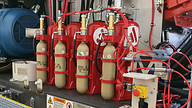
Ansul cartridge operated agent tanks
Cartridge operated tanks
Cartridge operated units store the extinguishing agent in a non-pressurised container and the propellant gas in a separate cartridge. When the system is activated, the propellant cartridge pressurises the agent tank. The pressure within the agent tank rises until the outlet rupture disc pressure is reached, thereby allowing the pressurised agent to be propelled through the distribution network. Cartridge operated tanks cannot be visually inspected to ensure they are properly pressurised.
Compaction
Settling and compaction (time consolidation) can occur over time in both stored pressure and cartridge operated tanks using dry chemical extinguishing agent. This is due to vibration on vehicles and mobile plant. While suppression agent tanks are designed to counteract this, excessive compaction can affect the performance of the fire suppression system and can cause it to fail.
The Ardent Dry Chemical powder uses high quality manufacturing techniques to produce a more finely milled powder. This milling process means that compaction is less severe, and the system is able to discharge easily and efficiently. Milling also contributes to the higher dispersion rates of the dry chemical agent, aiding coverage of the fire hazard areas.
Shock and Vibration
Shock and vibration are commonly observed on vehicles, especially off-road vehicles and plant. This is major concern to anything that is bolted to the vehicle, such as extinguishing agent tanks, and can lead to part failure, metal fatigue, and system failure. Thorough testing is needed to ensure they perform under these challenging conditions.
At Ardent, our in-house Research and Development team carefully analyse environmental conditions that may impact our fire suppression systems during the design process, ensuring that all of our systems are capable of withstanding the challenges.
Leakage
Loss of pressure can occur within fire suppression systems for a number of reasons, including manufacturing defects, damage to the system or shock and vibration. If propellant gas leaks are not detected, this could result in the pressure in the extinguishing agent tank dropping below the threshold for fire suppression system activation.
Inspection and testing
Just like the vehicles that they are designed to protect, all fire suppression systems require periodic inspection and maintenance. National Fire Protection Association (NFPA) Standard No. 17, the Standard for Dry Chemical Extinguishing Systems, outlines the monthly and semi-annual inspection requirements for both stored pressure and cartridge operated systems.
In addition, every 10 years all pressurised cylinders used in fire protection applications are legally required under the British/European Standard BS EN 1968:2002 to be hydrostatically tested. This tests the strength and integrity of the pressurised cylinder to ensure that they are in safe working condition. The responsibility for hydrostatic testing lies with the person in possession of the cylinder, and failure to test the cylinders can lead to fines of up to £5,000 and, in some cases, imprisonment.
This testing is vital for pressurised containers, as, over time, corrossion and cracking can cause cylinders to fail, leading to disastrous consequences such as explosions. In cases where a tank becomes damaged, it is also important to test the cylinder in order to ensure that is still in good, safe, working order.
Next blog post in the Vehicle Fire Suppression Basics Series: Fire Hazard Analysis
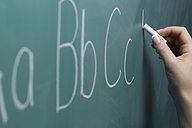
Fire Suppression Basics: Extinguishing Agents
We start this blog series with the essential component of any fire suppression system, the extinguishing agent.
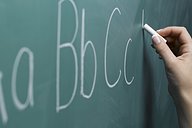
Fire Suppression Basics: Detection Systems
Even the most effective extinguishing agents depend upon a reliable detection system. Here we look at the most common types and their pros and cons.
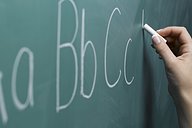
Fire Suppression Basics: Control Systems
Extinguishing agents and detectors are key components of any system, but it is the control module that dictates the response to fire.