Hanson UK produce aggregates, ready mixed concrete, asphalt and cement related products across over 300 sites around the UK. Production is key to their operations. If a machine was forced to stand down it would put a strain on operations and result in costly delays.
The problem
In an aggregate environment, machines work in harsh conditions, often for 7 days a week. Fires can happen spontaneously and without warning. Pressurised hydraulic lines can split and the atomized fluid can spray on to superheated surfaces such as the exhaust, manifold or turbo charger. Fires involving free flowing flammable liquids can ignite and spread quickly.
Having invested millions in new fleet equipment, Hanson wanted to protect operators and machinery and prevent fire incidents impacting on production.
Our solution
We’ve worked with Hanson for a decade so we have an in-depth understanding of their needs. We specified an electronically monitored system, which constantly checked for faults, as damage to fire suppression systems is a constant threat in such a rugged industry.
The system we specified was cartridge operated, which ensured powder was evenly discharged very quickly and efficiently. It was fully automatic, with a compact in-cab control module that allowed the driver to manually activate the system at any time. They could also delay the system so they had time to bring the machine to a safe stop. Tracked equipment only was also fitted with an electric stop and isolator, which isolated the batteries and stopped the engine in the event of a fire.
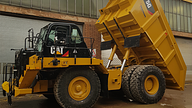
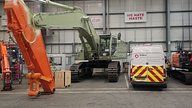